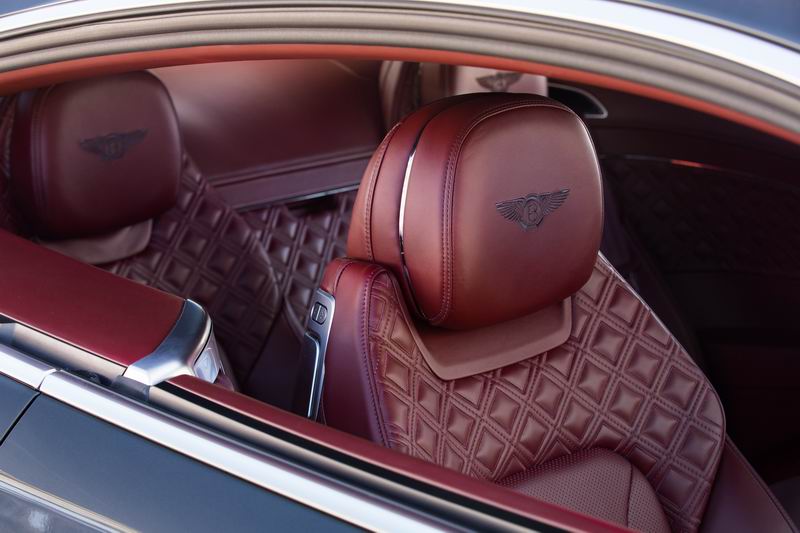
- BENTLEY’S UNIQUE DIAMOND-IN-DIAMOND QUILTING OFFERS UNIQUE INTERIOR PERSONALISATION OPTION FOR CUSTOMERS
- EACH DIAMOND REQUIRES 712 STITCHES, MASTERED BY A SPECIALLY-COMMISSIONED MACHINE, TO ACHIEVE THE PATTERN
- EXCLUSIVE DESIGN CONCEPT CREATED AS PART OF THE MULLINER DRIVING SPECIFICATION FOR THE NEW CONTINENTAL GT AND GTC
- DIAMOND-IN-DIAMOND QUILTING PROVES SO POPULAR IT IS NOW REINTERPRETED IN A FRESH STYLE FOR THE NEW FLYING SPUR
(Crewe, 23rd December 2019).- With an exact 712 stitches per diamond, Bentley’s striking Diamond-in-Diamond Quilting pattern for the interiors of the new Continental GT and Continental GT Convertible models is now ordered by three-quarters of all customers, as part of the Mulliner Driving Specification.
The Diamond-in-Diamond Quilting requires a high level of skill to produce and has a complex design story and manufacturing process. The pattern can be commissioned for all four seats, door casings and rear quarters. It is soft to the touch and truly stunning in appearance when viewed from both the inside and outside of the cars. Combining intricate stitching and embroidery, the unique quilting concept features a grid of elegant diamonds.
Initially designed for the Continental GT and GTC, the Diamond-in-Diamond concept adds a more sporting look to the cars’ interior, alongside the other elements of the Mulliner Driving Specification: 22” lightweight forged alloy wheels, embroidered Bentley emblems, additional veneer options, a jewelled-finish fuel filler, sports pedals and indented leather headliner.
A new quilting interpretation, inspired by the Diamond-in-Diamond technique is now being rolled out for Bentley’s new Flying Spur, launched in 2019. The new design features an elegant series of ever-lengthening diamonds tumbling down the seat, in precise yet seemingly random formation – this new technique uses the same machinery as the original Diamond-in-Diamond pattern.
Better by design
When redesigning the quilting for the Continental GT and GTC, Bentley designers were aiming to create something that could not easily be replicated. Bentley’s discerning customers are always looking for something unique and special, with depth to the craftsmanship – a concept that is hard to copy ensures this.
The Diamond-in-Diamond Quilting concept cannot, therefore, be mass produced, and requires specialist skill and bespoke machinery to execute.
The concept features a floating diamond within a main grid of larger diamonds. Unlike more simple or traditional quilting designs, the Diamond-in-Diamond requires more than just a simple sewing machine to complete the pattern, and cannot be achieved by hand. Specialist machine embroidery is employed, with a twofold result: solving the problem of how to achieve this complex pattern, as well as adding a new process that brings extra value in the highest level of craftsmanship.
The visible appearance of the Diamond-in-Diamond stitching is inherently shinier than the classic running stitch used in Bentley’s original quilting techniques and other forms of embroidery and stitching. The diamond stitches have a 3-dimensionality due to the quality of thread – the diamonds ooze luxury.
Diamond in the Rough
Bentley designers are always looking for balance. A diamond, or rhombus in Euclidean geometry, is a simple, universally recognised shape consisting of four equal-length diagonal sides. It stands as an emblem of Bentley’s signature design language, appealing in its simplicity and a playful shape for Bentley designers to work with. It is also reminiscent of Bentley’s iconic diamond knurling, seen throughout so much of its recent design history.
When Bentley Interior Designer Louise McCallum was tasked to redesign the quilting for the Continental GT and Continental GT Convertible, a twist on Bentley’s existing use of diamond patterns seemed a good place to start.
Louise recalls the development of the new quilting design: “It was seamless from start to finish, a really pleasurable process. The idea really drove itself along.” she says. “The Diamond-in-Diamond concept is intrinsically Bentley, and it is simple. It offers the potential for a multitude of colour options and the size of the diamonds can be altered, we can therefore see a future for this design as we can continue to freshen it up and innovate.”
When Bentley made its first prototype, the team attempted to individually tie off every single diamond by hand, using a simple sewing machine. This proved to be so labour-intensive and time-consuming that to continue to create this on a regular basis proved unfeasible. A new machine was essential…
Dream Machine
Bentley set about commissioning the bespoke design of a vast new embroidery machine with a digitally-led internal system – an exciting new investment for the factory site in Crewe.
Louise McCallum explains: “Process engineers in Bentley’s manufacturing department were all very on board with the challenge and enjoyed the chance to define a new machine, especially for the Diamond-in-Diamond concept.”
With the ability to tie off each diamond shape individually, the stitches created by the high-tech machine run fluidly with each shape. The machine is huge and can complete all areas of quilting in one go, incorporating a combination of technologies to form a complex web of running stitches. The machine can hold an entire ‘car set’ at one time (including every single quilted panel of the car interior), allowing it all to be sewn in unison. This ensures continuity and eliminates the chance of any minute colour discrepancies between different rolls of thread.
The computer input allows for complete flexibility on the shape and size of the diamonds. By hand, many different processes would be required to achieve the same effect and the diamonds would never be perfectly aligned to each square of the balanced grid they are set within. Like all aspects of Bentley’s exceptional craftsmanship, the result appears effortless, despite the complex level of detail behind the design.
The machine embroiders on a large scale, allowing for expansion and contraction of the leather. It is designed to fit every single colour of thread to allow for any colour combination under the rainbow. The endless possibilities mean that the technology is future-proof and able to cater to any new ideas conceived in the coming years. Customers find this level of personalisation allows them to make individualised choices when curating their new, dream car.
An Extraordinary Design Journey
While bringing the Diamond-in-Diamond concept to life on the drawing board and on leather samples was straightforward, executing the quilting within the car interior posed more of a challenge.
When a design is stitched into a piece of leather the surface shrinks as the quilting pulls the material away to form a mound, or ‘island’ as it is known by Bentley. This affects how each diamond must be spaced and the pattern needs to be bigger and smaller in certain places to strike balance. This diamond-shaped ‘island’ literally floats in a sea of leather creating a comfortable, soft quilt effect.
Further, the placing of the Diamond-in-Diamond pattern across the seats and door panels also provided its own design hurdles. The goal was to create a pattern that appears subtly elegant and perfectly balanced from any angle and to ensure a uniformity across all four seats. Despite many differences in the proportions, the types of head rest, among other things, the front and rear seats of a car all have to be designed in one go to make sure the design works throughout the car. Many different options were tested, adjusting the proportion, size and placing of each diamond fractionally each time until the perfect balance was achieved. The door panels and around the door handles proved particularly complex.
Bentley Head of Interior Design Darren Day comments: “It was a matter of trial and error. The art is actually ensuring that people don’t notice things at a first glance.”
The impact of the Diamond-in-Diamond Quilting on Bentley’s overall design ethos has been huge. It has opened up the possibility of more flexible design when it comes to quilting, moving away from a more traditional style (straight fluted lines on panels, created using simple sewing machines) towards a more free-thinking approach that is digitally processed and digitally led. The Diamond-in-Diamond Quilting will form a stitch in time in Bentley’s rich design and manufacturing history.
In July 2019, Bentley launched the EXP 100 GT: a vision for the future of the brand. This concept car contains elaborate quilting beginning with a grid of uniform stitching, flowing into a random pattern of embroidery, inspired by the Diamond-in-Diamond Quilting.
The Mulliner Driving Specification for the new Flying Spur also features a new diamond quilting design that uses a similar technique and the same machinery as the Diamond-in-Diamond, and has been inspired by this pattern.
For the discerning customer
Three-quarters of customers are now opting for the Mulliner Driving Specification in their Continental GT and GTC’s, which includes the Diamond-in-Diamond Quilting.
The colourways available are limitless, allowing Bentley to cater to all tastes – from a subtle shade of Portland or Beluga, to varying tones of one colour in gradient across the car, or even a rainbow of different colours for the bolder customer.
Bentley customers will always seek something unique and the Mulliner Driving Specification, including the Diamond-in-Diamond Quilting, caters to this in an exceptional fashion.
Explore in more detail in the Bentley Configurator.
Source: Bentley
Photograph: Bentley