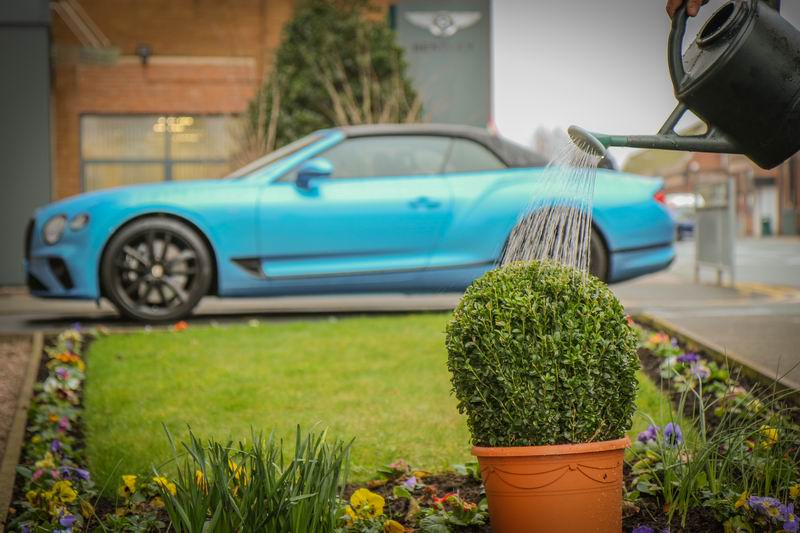
- BENTLEY’S PYMS LANE SITE INTRODUCES NEW WATER CAPTURE AND RECYCLING SYSTEM
- SYSTEM CAPTURES WATER FROM REVERSE OSMOSIS UNITS USED TO PURIFY WATER IN BENTLEY’S PAINTSHOP
- THE NEW APPROACH WILL RECYCLE OVER 350,000 LITRES OF WATER IN 2020 – ENOUGH TO MAINTAIN OUR GROUNDS AND CLEAN ALL 16 MILES OF OUR FACTORY FLOOR ROUTES
(Crewe, 24 January 2020).- Bentley Motors takes another step towards increasing its onsite sustainability with the successful pilot and launch of a new water recycling system at its site in Crewe.
Bentley aims to become the most sustainable luxury car manufacturer, and following its recent carbon neutral certification from the Carbon Trust, the company continues to invest in a range of technologies to help further reduce water use, energy use and the amount of CO2 emissions it offsets.
Bentley uses a number of reverse osmosis treatment units onsite to ensure that the water used in manufacturing processes is free of any contaminants that could affect the high quality paint finish Bentley cars are renowned for. The process works by using high-pressure pumps to separate contaminants and create pure water. Due to the level of purity required, previously, for every three litres of water drawn into the reverse osmosis treatment, only one could be used.
Thanks to the installation of the recycling systems, those two litres are now being captured and used to keep the factory and our grounds in a pristine condition.
Peter Bosch, Member of the Board for Manufacturing, explains:
“Our site in Crewe designs, engineers and manufacturers luxury cars for export all over the world. Water plays a vital part in a number of our manufacturing processes, but it’s also a natural resource, so reducing our consumption and reusing as much as we can is a key part of our philosophy. The new recycling systems we’ve installed help us to meet that objective – whilst still manufacturing cars of the highest quality.
“Our projections show that we can expect to capture over 350,000 litres of water in 2020, all of which can now be used to maintain our site. For example, we wash over 16 miles of internal routes every day to ensure that our factory is in immaculate condition – and look after our plants and grounds carefully.
“The project is a great example of the innovative thinking our colleagues are coming up with to reduce the impact of our site on the environment – and our next focus point will be to capture even larger volumes through rainwater harvesting.”
Source: Bentley
Photograph: Bentley